Electrophoretic Coloring
Also known as e-coating or electro-coating, this metal finishing technique is more akin to electroplating than it is to powder coating process. With electrophoretic deposition, the substrate of a metal is immersed in a liquid solution that may comprise an epoxy, paint, or some of the other water-based solutions. After that, an electric current is passed through to attract suspended particles in the bath, and thereby, deposit the same onto a substrate’s surface.
The coatings cover every nook and cranny because as the high spots become electro coated, they become insulated and divert the current to the low spots. Also the coatings are extremely thin.
The electrophoretic surface coating process provides the user with the following economical, technical and environmental benefits:,
Much better consistency in coating thickness as compared to powder coating
No wastage - almost 100% transfer efficiency.
Consistent, controllable film thickness, even on sharp edges and in awkward recesses.
Smooth films - no runs or sags.
Water based process - only small amount of low volatility solvent required.
Low temperature/time stoving schedules and upon its corrosion resistance (eg Al-Cu alloys) will give a useful measure of protection.
The coatings cover every nook and cranny because as the high spots become electro coated, they become insulated and divert the current to the low spots. Also the coatings are extremely thin.
The electrophoretic surface coating process provides the user with the following economical, technical and environmental benefits:,
Much better consistency in coating thickness as compared to powder coating
No wastage - almost 100% transfer efficiency.
Consistent, controllable film thickness, even on sharp edges and in awkward recesses.
Smooth films - no runs or sags.
Water based process - only small amount of low volatility solvent required.
Low temperature/time stoving schedules and upon its corrosion resistance (eg Al-Cu alloys) will give a useful measure of protection.
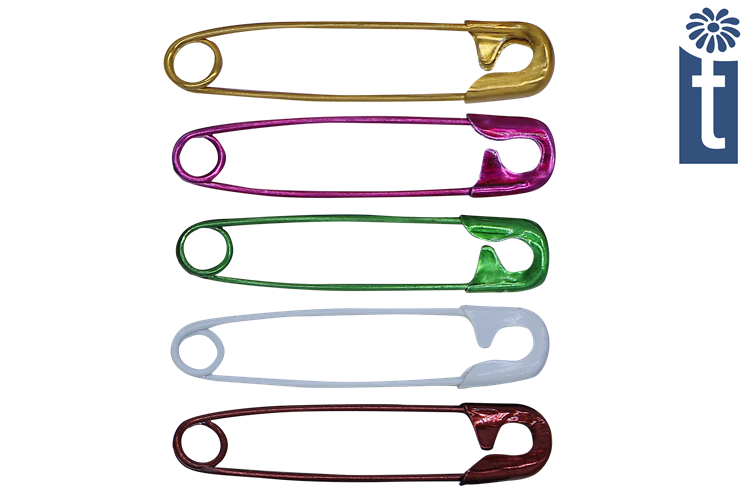