Zinc Plating
Zinc plating is an electroplating process for the corrosion protection of metal surfaces and it also increases their wear resistance.
Zinc electroplating process can be plated on any metal, but the most common ones are the iron and steel.
Advantages of Zinc Plating:
• Multiple passivate colors available• Excellent corrosion resistance
• ROHS Compliant options
• Can provide decorative finish
Methods available
1. Alkaline Zinc Plating2. Chloride Zinc Plating
We offer this finish in each of the following segments of our capabilities:
1.BARREL2.VAT
Alkaline Zinc VAT:
We offer zinc plating on VAT Method for items in Clear, Blue ,Yellow, Black, green passivate finishes (hexavalent & trivalent available) working within the RoHS Directive.
Benefits of Alkaline Zinc Plating:
1. Totally eco friendly and does not contain cyanides at all.2. The deposits from Alkaline Zinc have better uniformity and metal distribution. there by improved corrosion resistance.
3. No corrosive fumes.
4. Eliminates the use of poisonous Cyanide and also reduces the cost of waste treatment to destroy Cyanides.
5. Low current density coverage is excellent.
Zinc Chloride Barrel:
We have zinc plating barrels for items such as nuts, bolts, fasteners and brackets finishing in blue, clear, yellow, green, black with a capacity of up to 1000 kgs /per shift. We offer both hexavalent and trivalent coatings.
Benefits of Chloride Zinc Plating:
1.Acid zinc electroplating is one of the most important methods used for electroplating.2.It is a very cost effective process and is often used to provide a protective coating on automobile parts and textile parts.
Passivations available:
The term "passivation" quite simply means rendering a surface passive, or not prone to corrosive attacks when subjected to corrosive elements.
• Trivalent Clear (RoHS Compliant)• Trivalent Yellow (RoHS Compliant)
• Trivalent Black (RoHS Compliant)
• Trivalent blue(RoHS Compliant)
• Hexavalent Olive green
• Hexavalent Yellow
Important zinc plating benefits include excellent adhesion and its resistance to hydrogen embrittlement.
HYDROGEN DE-EMBRITTLEMENT:
We also offer a de-embrittling process which is essential for removing the hydrogen that has been deposited on the parts during the zinc plating and ensuring the parts do not become brittle.
During the cleaning and acid pickling process of electroplating, atomic hydrogen can be absorbed through the surface of the metal component. The electroplated coating traps the hydrogen inside the steel component unless they are baked soon after plating to drive the hydrogen out. If the hydrogen remains in the steel, it can migrate to areas of high stress and cause small micro cracks, which rapidly enlarge under load causing a brittlement failure.
Specifications offered
ASTM B633
This specification covers material and process requirements for electrodeposited zinc coatings applied to iron or steel articles to protect them from corrosion
BS EN ISO 2081:2008
BS EN ISO 2081 is the international standard that specifies the requirements for electroplated coatings of zinc with supplementary treatments on iron or steel.
IS 1573: 1986
Indian standard
Specification for electroplated coatings of zinc on iron and steel
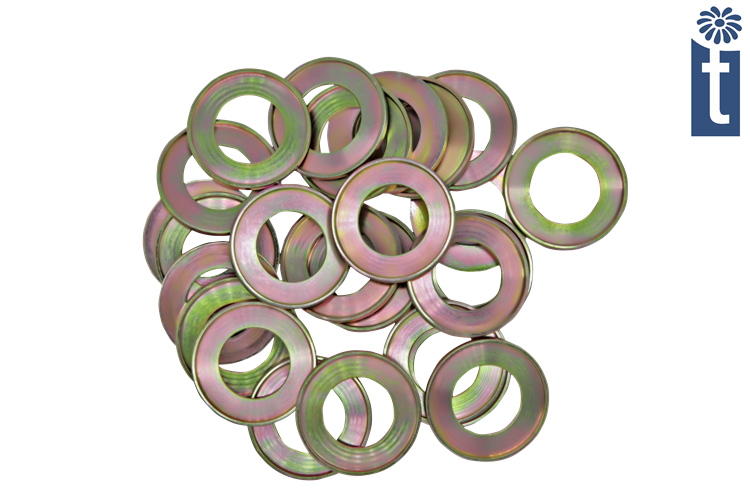
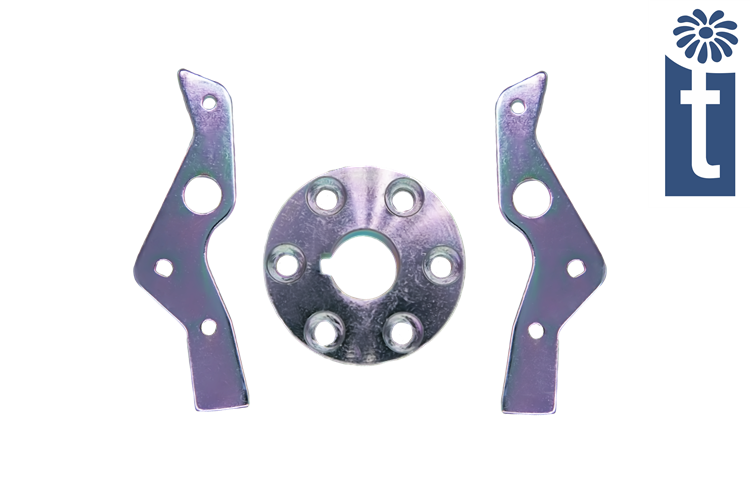
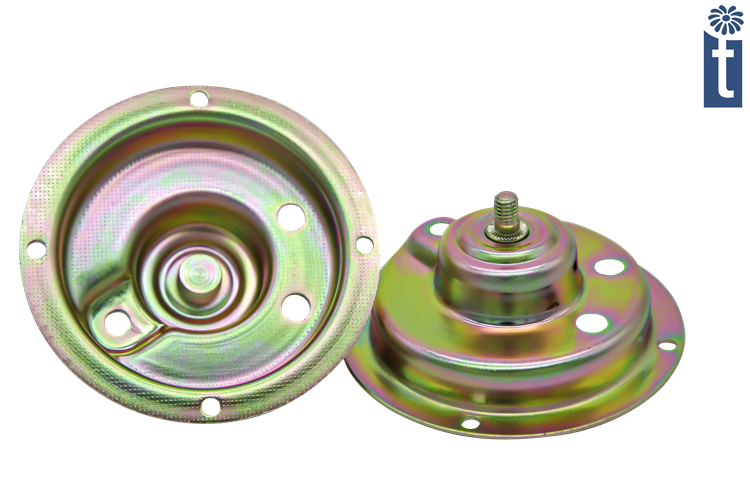
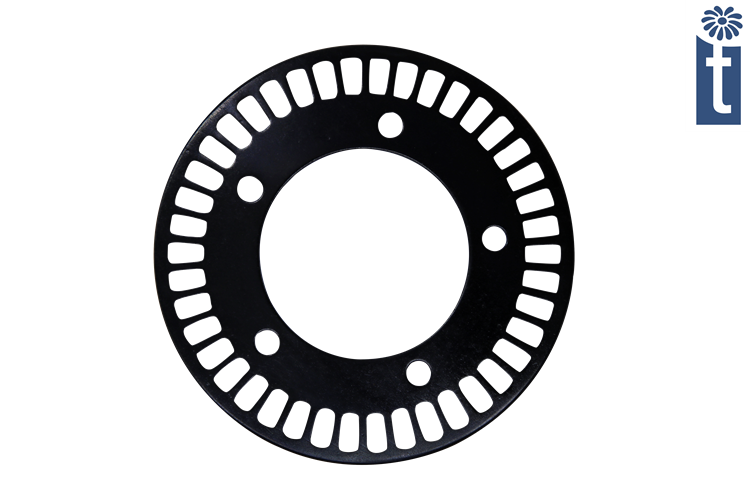
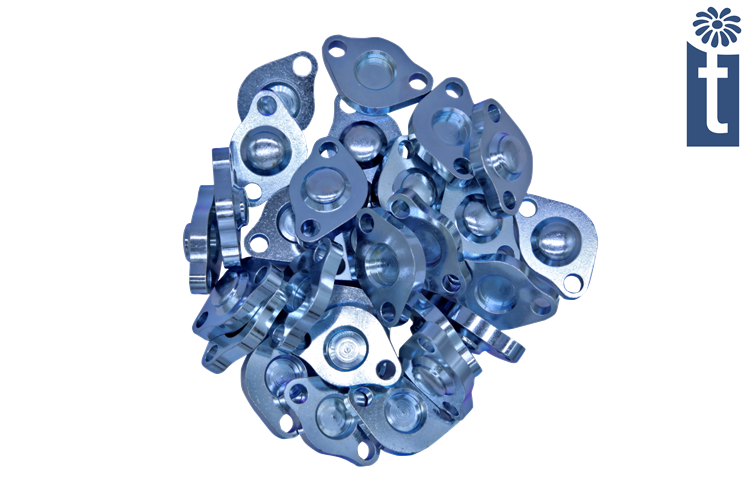
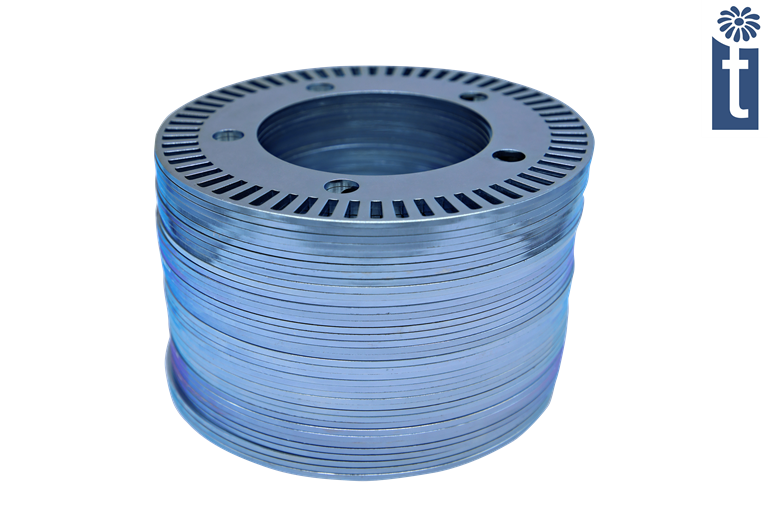